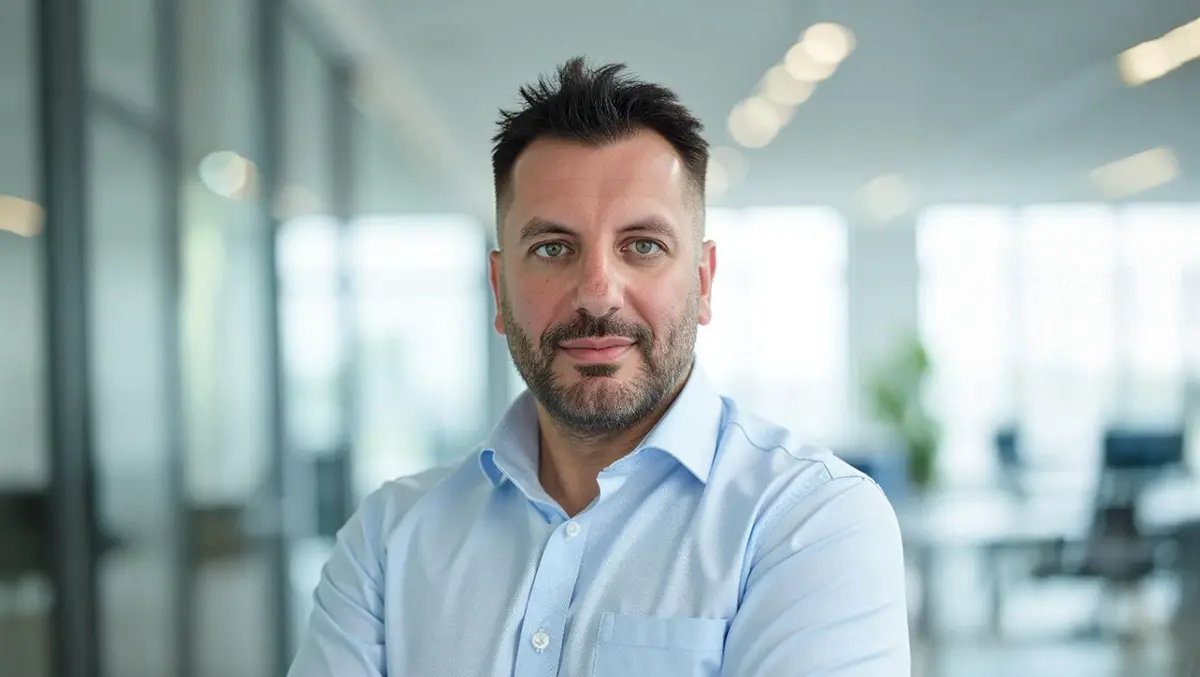
ERP success or ERP chaos: Why SMB manufacturers win or lose in implementation
In the race toward digital transformation, Enterprise Resource Planning (ERP) systems are increasingly seen by manufacturers as vital engines for growth, efficiency, and competitiveness.
In Australia and New Zealand, many small and mid-sized manufacturing businesses (SMBs) are still heavily reliant on manual processes. According to MYOB's Digital Disconnection Challenge report, nearly one in five businesses have little to no digitisation—often relying on spreadsheets to manage everything from inventory to production schedules. This digital gap presents both a challenge and an opportunity: those who modernise with ERP systems are better positioned to improve efficiency, reduce errors, and compete in a rapidly evolving market.
However, for those SMBs adopting modern digitisation, the road to ERP implementation is riddled with pitfalls. While success can unlock streamlined operations and real-time decision-making, failure can bring costly disruptions, spiralling budgets, and underwhelming returns.
According to Panorama Consulting's 2024 ERP Report, 97% of organisations report improved business processes after implementing ERP systems. However, Gartner estimates that more than 70% of these implementations fall short of their original business objectives.
The contrast is stark: ERP can either be a springboard for strategic growth or a costly misstep that takes years to correct.
Unlocking the potential
For manufacturers, the promise of ERP remains compelling. When successfully executed, organisations report sweeping improvements across their operations. Panorama's data reveals that 95% of businesses experience enhanced customer experience, while 91% see improved standardisation and lower IT maintenance costs.
Productivity gains, better supplier interactions, and access to real-time data are among the most widely reported benefits, and this operational coherence leads to more than just internal efficiency.
With silos eliminated, compliance improved, and inventory levels optimised, manufacturers find themselves better equipped to respond to market demands, support customer needs, and pursue growth initiatives.
Understanding the risks
Despite these benefits, ERP implementation remains one of the most complex IT undertakings a company can pursue. The challenges are multidimensional, involving not just technology, but people, processes, and culture.
Common risk areas include poorly defined project scopes, integration complications with legacy systems, and cybersecurity concerns. Operational disruptions during implementation and resistance to change among staff are also frequent hurdles.
When these issues are not managed proactively, the result can be missed deadlines, budget overruns, and underutilised systems.
A robust implementation strategy begins with realistic planning, supported by strong governance and risk mitigation. Flexibility, clear communication, and a willingness to adapt are just as crucial as selecting the right technology.
Where implementations go wrong
One of the most common and costly mistakes in manufacturing ERP projects is inadequate planning. Businesses often move forward without a clear vision of their operational model or measurable goals.
Without these guideposts, it becomes difficult to align the project with business needs, leading to missteps in vendor selection and system configuration.
Budget overruns also plague many implementations. Nearly one in four ERP projects exceed budget, driven by unanticipated technology requirements, underestimated staffing needs, and unexpected data challenges.
Often, organisations fail to account for the full scope of costs - including training, process redesign, and post-go-live support - leading to fiscal strain and, at times, project abandonment.
Training deficiencies further compound these issues. New systems often entail significant shifts in how employees do their jobs. But with compressed timelines and limited resources, training is often rushed or insufficient. Poor user adoption follows, undermining the system's value and productivity benefits.
Another technical pitfall lies in data migration. Transferring data from legacy systems can expose long-standing quality issues. Errors in data mapping or insufficient validation testing can ripple through the entire ERP platform, compromising operational accuracy from the start.
Best practices for success
Lead from the top.
Avoiding these pitfalls begins with leadership. Executive support must be visible and sustained throughout the entire implementation process.
Setting up a dedicated steering committee and maintaining clear governance helps keep the project aligned with strategic priorities. Also, timelines should be realistic and account for all project phases, including thorough testing and validation.
Plan for the people, Not just for the tech.
Adequate time for training, particularly role-specific instruction, is vital to ensure smooth adoption. This includes refresher sessions and ongoing support even after go-live.
Appointing internal champions with both technical and interpersonal skills can help bridge communication between teams and provide a single point of accountability. These champions should be empowered with decision-making authority and the resources necessary to lead change effectively.
Don't underestimate data readiness.
Equally important is data readiness. Early audits of existing data quality, followed by strict governance over cleaning and migration processes, can prevent post-launch issues. Manufacturers should collaborate closely with vendors to establish robust procedures for validation and testing.
Pick a partner, not just a vendor.
Vendor selection itself is also critical. Manufacturers should seek partners with proven experience in their specific industry and with similar-sized organizations. A good vendor will not only deliver the software but act as a strategic partner throughout the implementation lifecycle.
Change is a process.
Finally, change management should not be an afterthought. Structured communication, employee involvement, and recognition of success milestones help keep morale high and resistance low. Implementation is as much about people as it is about technology.
Looking ahead
ERP implementation is not merely a technology upgrade: it's a transformative business initiative. When approached thoughtfully, with a clear strategy and stakeholder engagement, ERP systems can unlock dramatic improvements in efficiency, insight, and customer experience.
For SMB manufacturers, the risks are real, but so are the rewards. The firms that thrive in this space are those that understand implementation as a journey: one that blends technical rigor with empathetic leadership and meticulous planning. ERP isn't just software — it's a future operating model. And for SMB manufacturers in Australia and New Zealand, getting it right means planning like it's business-critical. Because it is.